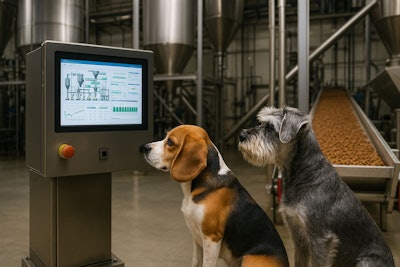
First, training and retaining skilled workers can challenge pet food producers. Then, after those laborers have worked for decades and gained extensive experience, they retire and take all that knowledge with them. Artificial intelligence tools can address this issue.
Matt Lueger, executive vice president of sales at NorthWind, and Bill Ward, founder and CEO of Northslope Technologies, discussed how pet food facility operators can use AI to address skilled labor shortages and knowledge transfer during Petfood Forum 2025.
Northslope and NorthWind collaborated to create an AI system that could learn from experienced operators and answer newer workers questions using a database of manuals, standard operating procedures and institutional knowledge. NorthWind brought their expertise in automation to the table and Northslope contributed their experience building customizable software tools. The first step in the collaboration was finding a problem to solve.
When we looked at our customers’ biggest concerns, labor difficulties came up repeatedly, Lueger said.
“The thing that kept coming to the top of the pile was ultimately a shortage of skilled labor,” Lueger said. “They had 30-year operators or maintenance people retiring, taking a lot of knowledge with them, or they couldn't add more sophisticated systems in their plants. They needed to be able to train people quickly, but they couldn't get skilled labor. It's hard to rertain, or just wasn't out there in the market.”
Northwind and Northslope focused on developing an AI assistant capable of capturing decades of operational knowledge and delivering it in real time to inexperienced staff. They aimed to create an AI system that would allow new operators and maintenance teams to diagnose and resolve production issues using natural language prompts.
The goal was to use AI to augment expertise, not replace it, Lueger said. If an experienced operator knows what a certain alarm means and how to fix it, the AI system can learn from that and guide newer staff through the same process.
Given the sensitivity of operational data, their team selected Palantir as the foundation for their AI expert tool. Palantir’s history with military and defense contracts made it a compelling choice for customers prioritizing data security.
Within Palantir, NorthWind and Northslope developed a layered AI application that serves two main purposes. The AI provides a searchable knowledge base built from manuals, SOPs and institutional knowledge. The system also has a root cause analysis tools that guide users through system faults and alarms.
One example involved an operator attempting to start a batch process who encountered a system halt. Rather than consult multiple documents or wait for expert support, the operator could use a prompt that identified the alarm source and offered step-by-step checks to resolve the issue.
Another example involved extruder startup. New users unfamiliar with the machine could ask, “How do I start the system?” and receive consolidated, sequential instructions culled from multiple documents, complete with reference links to visuals.
When to use AI in pet food production, and when not
The AI system isn’t for the 30-year veteran, Lueger said. It’s for the three-month operator who doesn’t even know where to find the right manual.
Ward emphasized that one should align AI capabilities with an existing need. Trying to bolt AI onto a workflow that doesn’t need it is a recipe for failure.
“You start with the problem you're actually trying to solve, then you work backwards to it and use the technology available,” he said.
While the current focus is on operations and maintenance, Ward sees opportunity to extend the platform into other areas such as production scheduling, supply chain optimization and mobile service support. The same platform they developed can be adapted to a range of uses. What’s more, the system can adapt to different facilities and operational procedures, which eliminated the need to build a custom software platform for each location.
“One of the most important takeaways from our learning experience here together is that you start with one problem, and then once you have that one problem solve something that costs a million dollars a year and that's impacting the budget, then you can start to think about where other places will have other 1 million dollar problems, and you can use all the same technology, a lot of the same data, all that data works together faster.”
For pet food manufacturers facing tight labor markets, retiring expert workers, increasing automation complexity and other issues, an AI system may be able to address various issues.